President Trump’s tariffs, and the uncertainty surrounding them, have caused many businesses to call a halt to major moves as they assess the situation (for example, both Klarna and StubHub have recently delayed their planned IPOs). But patch manufacturer World Emblem is moving full speed ahead with a manufacturing expansion to the Dominican Republic (DR), adding a new facility there in addition to an existing plant in Mexico that the company opened 18 years ago, as well as its U.S. manufacturing operations.
The DR is not just a business-friendly environment, it’s also a good place to operate from a tariff perspective, since the U.S. is currently running a trade surplus with the country. World Emblem, which supplies brands including Cintas, New Era, Vestis, Perry Ellis and Levi’s, is in the process of building a plant within a free-trade-zone complex in Santiago, DR, and also plans to use AI and automation to increase the productivity of its existing facilities.
Managing Growth without Expanding the Payroll
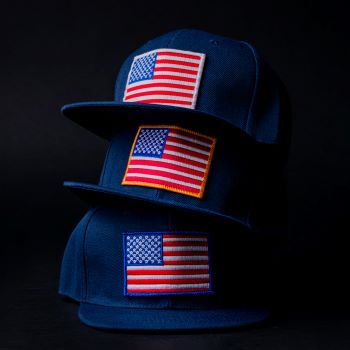
“We’re growing as an organization; we plan to double in size over the next five years, but we don’t want to double the number of people we employ,” said Jim Kozel, COO of World Emblem in an interview with Retail TouchPoints. Additionally, “we want to normalize [the impact of] tariffs and keep costs down to our customers,” he added. “It’s a three-legged effort. The move to DR is a quick fix; using AI and automation is a good fix; and our lean manufacturing and continuous improvement efforts are a long-term fix to both keep everyone employed and keep our costs where they need to be.”
The South Florida-based World Emblem employs 1,200+ people total — more than 800 of which are based at its Mexico facility in Aguascalientes ) — and produces close to 250 million products annually, including embroidered patches and emblems. The 450,000-square-foot Mexico plant runs six main production lines and uses “intricate equipment that would require a good bit of effort to move,” said Kozel, so pulling up stakes and attempting to re-create the plant in the DR was not a viable option. “I can’t visualize getting out of Mexico,” he added.
Advertisement
What will be moving to the new facility when it’s completed will be World Emblem’s supply chain of patch “blanks.” “All of our items are custom-made; there are no ‘in-stock’ items we can just pull from a shelf,” Kozel explained. “But we do use stock ‘blanks,’ and those are not made in Mexico,” meaning that with the change in tariffs, “it would add a good bit of cost to our primary lines in the U.S., and that’s hard to pass on to the customer.”
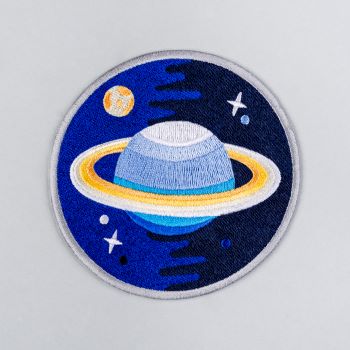
The tariff-free landscape in the DR, in contrast, will keep items made from these blanks “out of harm’s way,” as Kozel put it. It also helps that the DR “is working hard to work with companies to come in, to help build a manufacturing base on the island.”
Additionally, Mexico is no longer a cheap labor haven, and the rising costs of operating there already had World Emblem seeking different venues for expansion. “When we put in our first supply chain line in Mexico 18 years ago, Mexican labor was about $1.80 per hour,” said Kozel. Today, however, “Mexican labor is not cheap labor. The cost of doing business has changed when you add in things like transportation, the food we provide and having doctors and nurses there because of the number of people working there. We try to stay paired with the [Mexican] minimum wage, and the costs of shipping have gone up. All the tariffs have done was accelerated what we felt we had needed to do for several years.”
Adding Flexibility and Resilience to Manufacturing Processes
World Emblem already has done a fair amount of future-proofing its operations. If some event forces one of the company’s U.S. factories to halt production, “all of our designs are stored electronically, so all of our U.S. and Canadian facilities can produce the same item,” said Kozel. “If there’s a natural disaster or a labor issue, it gives you an awful lot of flexibility so customers don’t get affected at all.”
Additionally, World Emblem’s current and future investments in AI and automation on its production lines “have a very profound and quick effect,” said Kozel. “It’s like turning-on-a-light-switch fast; the minute you automate a line, it affects the people working on it.”
Kozel explained some of the many manual processes involved in creating patches to give a sense of the many steps that automation can shorten or eliminate: “The products are made with a ‘sandwich’ of materials that includes fabric and different types of films. There’s a lamination line that takes all the layers and melts them together. Eventually it’s taken to the chopper, which is 100% done by hand. The only thing that’s automated on [this type of line] are the heat rollers.”
The company also has been using continuous improvement methods — an ongoing process of analyzing performance, identifying opportunities and making incremental changes — but impacts from these efforts typically don’t start to pay off immediately. “We’ll hit more than a 12% improvement this year; we’re on track for it,” said Kozel. “We know what we’re going to get out of the projects we have going.”